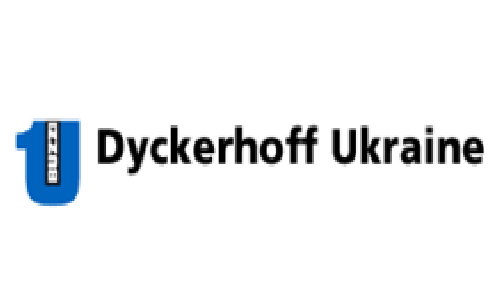
Dyckerhoff is an international manufacturer of cement and concrete. The company is a member of the Buzzi Unicem Group.
The main activity of the company is carried out at its own enterprises in Germany, USA, Luxembourg, Czech Republic, Poland, Russia, and Ukraine. Our strategy is to steadily increase profitability, optimize quality and improve products based on sustainable business development.
From January 1, 2016, cement companies merged into one legal entity — Dyckerhoff Cement Ukraine Limited Liability Company with Volyn-Cement and Yugcement branches.
«Dyckerhoff» in Ukraine seeks to combine the experience of «Dyckerhoff» in the world market, traditional German quality, stability, and reliability with the potential and skill of Ukrainian cement workers. To achieve this goal, Dyckerhoff in Ukraine carries out a comprehensive reconstruction of the Volyn-Cement and Yugcement branches in order to improve the environmental and economic standards of their activities and improve product quality.
Most of the transportation is carried out by road transport, and our company is faced with the problem of quality task solution in transportation management.
To solve the problems of vehicle logistics automation, we have chosen the company «Art Port», which has provided a software package «Art:Vehicle».
During the implementation of «Art:Vehicle» developers had to solve the following tasks:
- Synchronization of accounting for the vehicle work on the basis of trip sheets;
- Synchronization of cost accounting for vehicle repair.
Art Port specialists have conducted a survey of our company’s business processes, refined and implemented the software product, conducted training and further consultation of our employees.
During the implementation of the software product «Art:Vehicle» the following works have been performed:
- Synchronization of accounting for the vehicle work on the basis of trip sheets — work statistics, POL movement (refueling, consumption rate, and actual one);
- Integration of the accounting system «Art:Vehicle» with the production system;
- Automatic creation of trip sheets taking the consignment note into account;
- Calculation of tires and batteries;
- Calculation of income from cargo transportation;
- Synchronization of cost accounting for vehicle repair.
Implementation period: 1 month
Assessment on a 5-point scale:
— Compliance with the needs of the organization: 5
— Ease of working with the program: 5
— Assessment of the quality of the partner’s work: 5
The specialists of Art Port have approached the task set responsibly and taken the peculiarities of our work into account. We thank the director and employees of the company and recommend it as a reliable partner in the field of automation of industry solutions for automotive logistics.