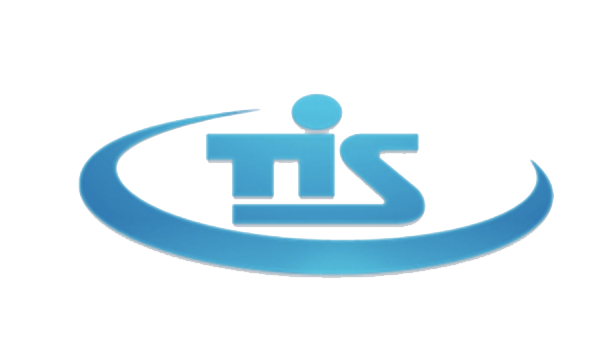
The largest infrastructure company TIS owns and manages the entire servicing infrastructure of terminals, including its own railway station.
TIS terminals are accessible to international markets for the production and consumption of grain, fertilizers, coal, ore, and consumer goods for hundreds of millions of people. About 700 vessel calls per year connect TIS with more than 1,500 ports worldwide. Our cargo turnover in 2017 amounted to 26.012 million tons.
LLC «TIS-Ruda» is the largest and most efficient export terminal of the Yuzhny port for the transshipment of iron ore pellets. Transshipment volume in 2017 exceeded 5.6 million tons.
The TIS-Ruda terminal in the Yuzhny seaport is a strategic link in «Ferrexpo» export logistics, the company is a co-owner of the terminal.
In connection with changes in the structure of the enterprise, it was decided to automate operational accounting.
To solve the problems of automating business processes, the LLC «Art Port» company proposed to adapt and implement software products of the «Art:Port» complex: «Art:Stevedoring» and «Art:Forwarding».
Specialists of the company “Art Port” finalized and implemented the software package, conducted training for the company’s operational staff. Our employees receive quality advisory support on the optimal use of these products.
As a result of the implementation, the following program sections are automated and adapted:
1. Block of dispatching control:
— documents of registration of railway waybills, wagon arrival at the station, and spotting to the port;
— a mechanism of wagon data loading from an Excel file of a wagon list from the station with the document formation of the railway bill, the wagon arrival at the station, and the acceptance certificate;
— a functional development to automatically change the wagon data in all documents after the railway bill adjusting the information in it;
— the AWP «Vessel arrival» was developed for simplified registration of the vessel approach schedule and vessel approach declarations;
— a mechanism has been implemented for taking into account the distance from the bow and stern of the vessel to the borders mooring at the berth;
— development of a mechanism for accounting of a step-by-step vessel loading plan in the «Cargo Plan» document in addition to the standard generalized cargo plan table;
— Adapted printed forms of the cargo plan — brief one with weight and deployed one in directions for each type;
— The document «Change-daily plan» has been developed with a printed form and a comparison of the plan and the fact in the context of equipment.
2. Block of the accounting group:
— the adaptation of the system for accounting bulk-loaded cargoes;
— to eliminate the problem with negative balances during dispatching, the separation of documentary and physical balances of cargo at the warehouse was carried out according to directions and contracts;
— development of the form “Register formation of cargo receipt” for automatic register generation of accepted cargoes for the period in the context of acceptance acts;
— development of a vehicle unloading workstation for quick registration of carriage processing with automatic generation of a document for wagon spotting to the port and in the printed form “Station Notification”;
— a reflection mechanism of the direct option of transport unloading onto the vessel for two situations has been implemented:
1. Unambiguous write-off of documents for the actual vessel;
2. Document registration to the warehouse instead of documents written off by FIFO to the vessel (the difference between the physical and documentary sections of the account);
— registration of dispatching to a vessel is divided into two tables: physical warehouse accounting by stockpiles, holds and accounting in cargo directions;
— a mechanism has been developed for cargo writing off on the basis of the Instructions in the orders for dividing one country of destination in the header of the order (according to the Customs Declaration) into several countries and contracts according to the instructions of the consignor;
— a mechanism of indicating in the order of the rules for cargo lot selecting in directions for dispatching;
— selecting cargo in the “Dispatching to the vessel” a mechanism of cargo selecting has been developed according to the Instruction of the consignor with the contract number and warehouse number where the cargo is located;
— change in the automatic selection of documents of consignments in the “Delivery Act” in connection with it, document write-off by arrival lot without the need to register displacement;
— development of the inventory subsystem: acts of inventory, write-off, and cargo registration with printed forms;
— A block of reports was implemented following the model of LLC «TIS-Ruda»;
— The possibility of cargo storage calculating has been improved according to the list of documents of lots from the selected delivery certificate.
3. Block of port logistics and forwarding:
— integration of the port forwarding subsystem in the main configuration «Art:Stevedoring»;
— an adaptation of the document “Monthly delivery plan” to the form accepted at the enterprise;
— adding a daily schedule of the wagon spotting with a changing the number of columns of days on the form depending on the month;
— development of the document «Annual Cargo Processing Plan»;
— a block of analytical reports has been developed: «Analysis of the railway transport processing», «Analysis of the warehouse usage»;
— development of printed forms based on samples for the port forwarding block: “Order for loading”, “Bill of lading”, “Mates receipt”, “Manifesto”, “Timesheet”;
— adding to the order for loading the field “Type of document of closing” (Bill of Lading, Mates receipt, Sea waybill).
A mechanism has also been developed for the work of the logistician — a special document in which it is possible to enter the planned indicators of the terminal work, and from the form — open the Excel file, which will be partially filled with the actual indicators from the database, but in addition, the user will be able to use any formulas, graphs and other objects, and then save it directly to the database in order to access the progress report of past periods at any time.
Implementation period: 3 months
Score on 5 point scale:
— Compliance with the needs of the organization: 5
— Convenience of work with the program: 5
— Evaluation of the quality of work of the partner «SAB»: 5
Specialists of the company “Art Port” arrived at the implementation of tasks with responsibility and took into account the features of our work.
The automated accounting system “Art:Stevedoring” made it possible to obtain convenience and functionality in the data processing.
Convenience starts already from the first steps of use — by loading wagon data from a wagon list’s Excel file from the station, the time for entering wagon data is significantly reduced. Thus, the risk of making mistakes is minimized.
Unloading vehicles at the “Vehicle Unloading Workstation”, is enough for a group of wagons to choose a storage location once, and the system will automatically create a document “Spotting/picking of wagons” reflecting the time of application submission, spotting, picking, as well as the beginning and end of unloading.
Also, the automated system creates a single information space by combining into a single data entry process by the operator of the dumping machine, accounting group, dispatching control, freight forwarding, and logistics group.
The fact of receipt and cargo dispatching are reflected in one place and are available to all interested users. Multiple input of the same data is eliminated.
The advantage of an automated accounting system is:
— elimination of manual document preparation — all documents are generated and printed from the program;
— “transparency” of accounting — each incoming/outgoing document (order, freight plan, shift-daily plan, bill of lading, manifesto) corresponds to an electronic analog with links to each other and a subordination structure, so it is possible always quickly to find the information of interest;
— increasing the accuracy of the received reporting documents — when generating reports the same data are used;
— Search and correction of errors as simplified as possible. If an error is found in the report, then when you open an electronic document in it, you can make changes;
— reduction of the time for preparation of reporting documents for the “closing” of the month;
— Any reports can be generated in real-time. Also, these reports can be independently changed by users without the involvement of Art Port specialists, and generated in different versions depending on the requirements;
— due to the “implementation” of the Instructions to the order, the procedure for documented movement of cargoes between warehouses is practically excluded;
— loading the vessel with actual data by the warehouse (CPU operator) and documents according to the instructions of the consignor (accounting group), it is possible to view the actual remnants of the warehouse in real-time and determine the difference.
LLC «Tis Ruda» expresses gratitude to the director and employees of Art Port for their qualified work on the development and implementation of the software package and plans to continue cooperation with this company in the near future in the following areas:
— cargo accounting outside the cargo turnover;
— Automation of the automated workplace of the CPU operator (assistance in making a decision: place selection of dispatching according to the balances in the warehouses, cargo requirements by orders, holds by the cargo vessel);
— accounting of equipment work;
— connection with the system of automatic identification of wagons.